The Cost Accounting Solved Paper 2011 Punjab University BCOM ADC II covered crucial topics such as material cost, labor costing, and process costing. It included detailed solutions for calculating Material Costing such as Economic Order Quantity (EOQ) and managing labor costs through time rate and piece rate systems. The process costing section provided step-by-step methods for assigning costs using weighted average, LIFO and FIFO. Financial statement preparation focused on cost sheets and operating expense statements. Additionally, the paper addressed budgeting and variance analysis, demonstrating practical applications to enhance managerial decision-making. These solved examples are essential for mastering cost accounting principles and practices.
Cost Accounting Solved Paper 2010 Punjab University BCOM ADC II
Paper Solved by Iftikhar Ali, Lecturer Statistics, Accounting & Finance
Table of Contents
Cost Accounting Solved Paper 2011 Punjab University BCOM ADC II
Q.1: Define cost accounting. How does it differ from financial accounting?
Answer:
Cost Accounting
Cost accounting is a branch of accounting focused on capturing a company’s total cost of production by assessing the variable costs of each step of production as well as fixed costs, such as rent expense. The process forms the basis for recording, classifying, analyzing, summarizing and allocating costs associated with an activity (CIMA) or a process as well as working out alternative courses of action to control these costs.
Key Characteristics of Cost Accounting:
Detailed Cost Information: It gives elaborate cost information regarding the production process, departments, and other centers of costs.
Internal Focus: Such methods, of course, are used for internal decision-making purposes, as they would help management in budgeting and cost control as well as in appraising the performance.
Types of Costs: Accounts for various costs like cost, direct overhead, indirect overhead, fixed and variable cost operating outgo etc.
Methods and Techniques: Uses different approaches and tools like standard costing, marginal costing, activity-based costing and job costing to understand as well as control cost.
How Cost Accounting Differs from Financial Accounting:
Purpose
Cost Accounting: As an offensive measure to assist management in decision making, cost control and performance enhancement.
Financial Accounting: The purpose is to give financials information for the all external stakeholders such as investors, creditors or regulatory authorities.
Users
Cost Accounting: Information which is used internally by managers and staffs of the organization.
Financial Accounting: Use by external parties, such as shareholders, analysts, regulators and creditors.
Regulation
Cost Accounting: No standardization, it provides flexibility and allows for internal management adaptation.
Financial Accounting: Regulated by standard frameworks like GAAP and IFRS
Reporting
Cost Accounting: In cost accounting, reports are more specific to segments or departments and processed within the department.
Financial Accounting: In financial accounting reports are prepared at aggregate level periodically which represents the financial position for the overall organization.
Content
Cost Accounting: Focuses on cost-related data and analysis, helping in budget preparation, cost control, and performance evaluation.
Financial Accounting: Focuses on the financial results of the entire organization, including profit and loss statements, balance sheets, and cash flow statements.
Time Orientation
Cost Accounting: Can be both historical (actual costs) and forward-looking (budgets, forecasts).
Financial Accounting: Primarily historical, recording past financial transactions.
By emphasizing internal efficiency and detailed cost analysis, cost accounting helps management make informed decisions to optimize resource allocation and improve profitability, whereas financial accounting ensures transparency and accountability to external stakeholders by providing a clear picture of the company’s overall financial health.
Q.2: Cost accountant of THAL Manufacturing Company has prepared following summary: Inventories at 1st July, 2010…….Required: Prepare a statement of Cost of Goods Sold.
Q.2: Cost accountant of THAL Manufacturing Company has prepared following summary: Inventories at 1st July, 2010:
Rs. | |
Raw materials | 30,000 |
Work in process | 18,000 |
Fuel | 2,000 |
Factory repair parts | 1,000 |
Finished goods | 13,000 |
During the month following transaction took place | |
Raw material purchased | 130,000 |
Fuel purchased | 18,000 |
Direct labour | 120,000 |
Miscellaneous factory overhead | 4,000 |
Repairs of factory (including purchase of parts) | 5,000 |
Depreciation of plant | 3,000 |
Superintendence | 2,000 |
Transportation out | 2,000 |
Purchase discount lost | 1,000 |
Indirect factory labour | 3,000 |
Inventories at 31st July, 2010: | |
Raw materials | 32,000 |
Work in process | 22,000 |
Fuel | 3,000 |
Factory repair parts | 2,000 |
Finished goods | 18,000 |
Required: Prepare a statement of Cost of Goods Sold.
Solution:
Thal Manufacturing Company
Schedule of cost of goods manufactured and sold
For the month ended 31st July 2010
Direct Material: | ||
Opening Raw materials | 30,000 | |
Add Purchases | 130,000 | |
Raw Material Available for use | 160,000 | |
Less Closing Raw Material | (32,000) | |
Raw Material Consumed (1) | 128,000 | |
Add Direct labour (2) | 120,000 | |
Prime Cost (1+2) | 248000 | |
Add Factory Overhead (W1) | 33,000 | |
Total Cost of Goods Manufactured | 281,000 | |
Add opening WIP | 18,000 | |
Cost of Goods to be Manufactured | 299,000 | |
Less Closing WIP | (22,000) | |
Cost of Goods Manufactured | 277,000 | |
Add Opening Finished Goods Inventory | 13,000 | |
Cost of Goods Available for Sale | 290,000 | |
Less Closing Finished Goods Inventory | (18,000) | |
Cost of Goods Sold | 272,000 |
Working 1: Calculation of Factory Overhead Cost
Fuel | ||
Opening Inventory Fuel | 2000 | |
Add Fuel purchased | 18,000 | |
Fuel Available for used | 20,000 | |
Less Closing Inventory Fuel | (3000) | |
Fuel Consumed | 17,000 | 17,000 |
Factory repair parts | ||
Opening Inventory Factory repair parts | 1000 | |
Add Repairs of factory (including purchase of parts) during the year | 5000 | |
Repair Parts Available for use | 6000 | |
Less Closing Inventory Repair Parts | (2000) | |
Repair Parts Consumed | 4000 | 4000 |
Others | ||
Miscellaneous factory overhead | 4,000 | |
Depreciation of plant | 3,000 | |
Superintendence | 2,000 | |
Indirect factory labour | 3,000 | |
Total Others | 12,000 | 12,000 |
Total Factory Overhead | 33,000 |
Q.3: Annual estimated Factory Overhead of a company for an expected volume of 180,000 pounds of a product was as follows: Fixed Overhead Rs. 36,000, Variable Overhead Rs. 108,000, Output was 10,000 pounds in June and actual overhead expenses were Rs. 7,700. REQUIRED: (1) The overhead rate per unit. (2) Spending variance (3) Idle capacity variance.
Solution:
(1) The Overhead Rate per unit/FOH Applied Rate
\[ \mathbf{FOH\ Applied\ Rate\ = \ }\frac{\mathbf{Estimated\ FOH}}{\mathbf{Expected\ Volume}}\ \]
\[ \mathbf{FOH\ Applied\ Rate\ =}\frac{\left( \mathbf{Fixed\ FOH\ + \ Variable\ FOH} \right)}{\mathbf{Expected\ Volume}}\ \]
\[ \mathbf{FOH\ Applied\ Rate\ =}\frac{\left( \mathbf{36,000\ + \ 108,000} \right)}{\mathbf{180,000}}\ \]
\[ \mathbf{FOH\ Applied\ Rate\ }\mathbf{=}\frac{\mathbf{144000}}{\mathbf{180000}}\mathbf{= 0.8\ Per\ Pound}\ \]
(2) Spending Variance.
Budgeted FOH for Capacity Attained: | |
Fixed FOH + (Capacity Attained x Variable Rate) W2 | |
3000 W2 + (10,000 x 0.6) W1 | 9000 |
Less Actual FOH | (7700) |
Favorable | 1300 |
(3) Idle Capacity Variance.
Applied FOH W3 | 8000 |
Less Budgeted FOH for Capacity Attained | (9000) |
Unfavorable | (1000) |
W1: Variable Rate
\[ \mathbf{Variable\ Rate =}\frac{\mathbf{Expected\ Variable\ FOH}}{\mathbf{Expected\ Volume}}\ \]
\[ \mathbf{Variable\ Rate}\mathbf{=}\frac{\mathbf{108000}}{\mathbf{180000}}\mathbf{= 0.6}\ \]
W2: Monthly Fixed Rate
\[ \mathbf{Fixed\ FOH\ Monthly\ Rate =}\frac{\mathbf{36000}}{\mathbf{12}}\mathbf{= 3000}\ \]
W3: Applied FOH
\[ \mathbf{Applied\ FOH = Capacity\ Attained\ \times FOH\ Applied\ Rate}\ \]
\[ \mathbf{Applied\ FOH = 10,000\ \times 0.8 = 8000}\ \]
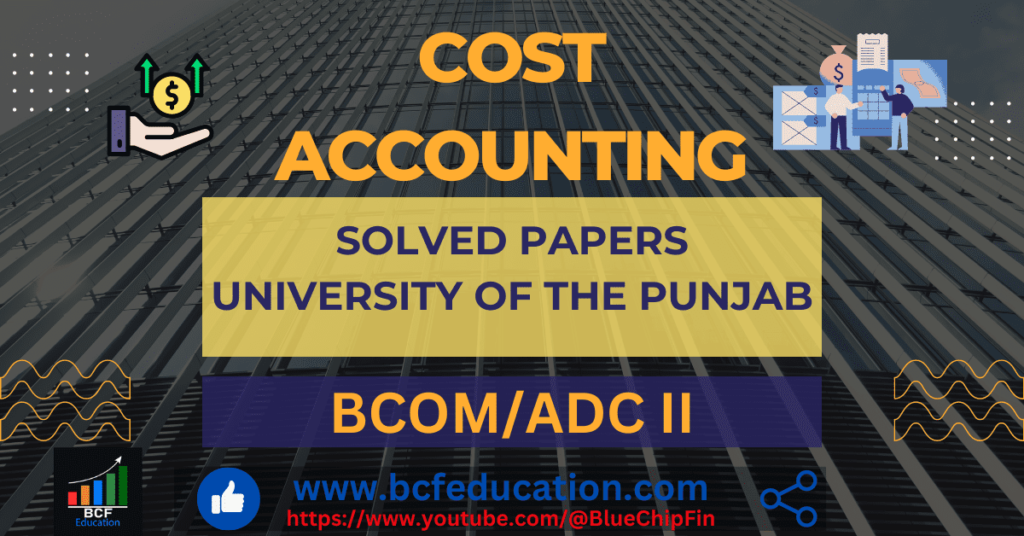
Q.4: A company received an order for 1,000 instruments at a sales price of Rs. 75 per instrument. Costs incurred to manufacture these instruments were……Required: Entries that would appear in the books under each of the following conditions (i) When reworking costs are charged directly to the job on which they occurred. (ii) When additional costs incurred in reworking are charged to factory overhead account.
Q.4: A company received an order for 1,000 instruments at a sales price of Rs. 75 per instrument. Costs incurred to manufacture these instruments were:
Direct materials Rs. 20 per instrument
Direct labour Rs. 10 per instrument
Manufacturing overhead was applied @ 200% of direct labour cost.
On final inspection it was found that 200 instruments were defective which were returned to concerned department of factory for rework. The additional costs for this rework were:
Direct labour Rs. 1000
Manufacturing overhead at applied rate.
Required: Entries that would appear in the books under each of the following conditions:
- When reworking costs are charged directly to the job on which they occurred.
- When additional costs incurred in reworking are charged to factory overhead account.
Setup entries in two parallel columns for the following:
- To record initial cost of manufacturing the order.
- To record the additional costs for correcting the defective work.
- To record the completion of the order.
- To record the shipment of the order to the customer.
Solution:
(i) When reworking costs are charged directly to the job | (ii) When additional costs incurred in reworking are charged to factory overhead | |||||||
a | W.I.P– Materials | 20,000 | a | W.I.P– Materials | 20,000 | |||
W.I.P– Labour | 10,000 | W.I.P– Labour | 10,000 | |||||
W.I.P– F.O.H | 20,000 | W.I.P– F.O.H | 20,000 | |||||
Materials | 20,000 | Materials | 20,000 | |||||
Payroll | 10,000 | Payroll | 10,000 | |||||
F.O.H Applied | 20,000 | F.O.H Applied | 20,000 | |||||
b | W.I.P– Labour | 1,000 | b | F.O.H Control | 3,000 | |||
W.I.P– F.O.H | 2,000 | Payroll | 1,000 | |||||
Payroll | 1,000 | F.O.H Applied | 2,000 | |||||
F.O.H Applied | 2,000 | |||||||
c | Finished Goods | 53,000 | c | Finished Goods | 50,000 | |||
W.I.P– Materials | 20,000 | W.I.P– Materials | 20,000 | |||||
W.I.P– Labour | 11,000 | W.I.P– Labour | 10,000 | |||||
W.I.P– F.O.H | 22,000 | W.I.P– F.O.H | 20,000 | |||||
d | Cost of goods sold | 53,000 | d | Cost of goods sold | 50,000 | |||
Finished Goods | 53,000 | Finished Goods | 50,000 | |||||
Accounts Receivable | 75,000 | Accounts Receivable | 75,000 | |||||
Sales | 75,000 | Sales | 75,000 | |||||
Q.5: Ramdan Company had its factory in Karachi but its head office is in Lahore. On October 1st 2010, the Factory trial balance appeared as follows…….Required: Journal entries to record the above transactions on the general office and on the factory office books.
Q.5: Ramdan Company had its factory in Karachi but its head office is in Lahore. On October 1st 2010, the Factory trial balance appeared as follows:
Rs. | Rs. | |
Materials | 30,000 | |
Work in process | 80,000 | |
Finished Goods | 40,000 | |
Factory Overhead Control | 580,000 | |
Factory machinery | 240,000 | |
Accumulated depreciation on factory machinery | 72,000 | |
Applied factory overhead | 569,000 | |
General Ledger | 329,000 | |
Total | 970,000 | 970,000 |
The following transactions were complete during October:
- Direct materials Rs. 100,000 were purchased on terms 2/10, n/30.
- The factory payroll for Rs. 75,000 direct labour and Rs. 15,000 indirect labor was mailed to the home office. The home office payroll was Rs. 20,000 for sales salaries and Rs. 30,000 for general office salaries. Employees’ payroll deductions were recorded at the home office at the following rates:
15% of Gross earnings for Income Tax;
10% of Gross earnings as provident fund contribution by the employees.
- Materials requisitions were as follows:
Rs. | |
Direct materials | 70,000 |
Indirect material | 8,500 |
Shipping supplies | 1,500 |
- Indirect factory materials and supplies amounting to Rs. 25,000 were purchased.
- Defective indirect materials returned to the supplier amounted to Rs. 1,000.
- Sundry factory expensed of Rs. 8,300 were recorded.
- Depreciation of an annual rate of 10% of the original cost was recorded on the factory Machinery.
- Accounts payable totaling Rs. 210,000 including the accrued payroll, were paid.
- Factory overhead was applied to production at the rate of Rs. 6 per direct labour hour; the Factory worked 7,000 hours.
- Goods completed with a total cost of Rs. 215,000.
- Goods costing Rs. 200,000 were sold for Rs. 274,000.
Required: Journal entries to record the above transactions on the general office and on the factory office books.
Solution:
(b) (i) | Payroll | 140,000 | |
Income Tax | 21,000 | ||
Provident Fund | 14,000 | ||
Accrued Payroll | 105,000 | ||
(Deductions & Payroll Recorded) | |||
(ii) | Accrued Payroll | 105,000 | |
Voucher Payable | 105,000 | ||
(Voucher Payable for accrued payroll) | |||
(iii) | Factory Payroll | 90,000 | |
Selling Expenses | 20,000 | ||
Administrative Expenses | 30,000 | ||
Payroll | 140,000 | ||
(Distribution breakup for total payroll) | |||
(c) | Selling Supplies | 1500 | |
Factory Ledger | 1500 | ||
(Shipping Supplies issued from store) | |||
(d) | Factory Ledger | 25,000 | |
Voucher Payable | 25,000 | ||
(Indirect Material & Supplies purchased & sent) | |||
(e) | Voucher Payable | 1000 | |
Factory Ledger | 1000 | ||
(Defective material returned) | |||
(f) | Factory Ledger | 8300 | |
Voucher Payable | 8300 | ||
(factory overhead recorded) | |||
(g) | No Entry | ||
(h) | Accounts Payable | 210,000 | |
Cash | 210,000 | ||
(payable amount paid) | |||
(i) | No Entry | ||
(j) | No Entry | ||
(k) | Cost of Goods Sold | 200,000 | |
Factory Ledger | 200,000 | ||
(Cost of goods sold recorded) | |||
Accounts Receivable | 274,000 | ||
Sales | 274,000 | ||
(Goods sold on account) | |||
Total | 1104,800 | 1104,800 |
Factory Office Book
(a) | Material | 100,000 | |
General Ledger | 100,000 | ||
(Material received) | |||
(b) | W.I.P | 75,000 | |
F.O.H Control | 15,000 | ||
General Ledger | 90,000 | ||
(Factory payroll Recorded) | |||
(c) | W.I.P | 70,000 | |
F.O.H Control | 8500 | ||
General Ledger | 1500 | ||
Materials | 80,000 | ||
(Material issued from store) | |||
(d) | Materials | 25000 | |
General Ledger | 25000 | ||
(Indirect material received) | |||
(e) | General Ledger | 1,000 | |
Materials | 1,000 | ||
(Defective material returned) | |||
(f) | F.O.H Control | 8300 | |
General Ledger | 8300 | ||
(Sundry factory expenses recorded) | |||
(g) | F.O.H Control | 24,000 | |
Factory Machinery | 24,000 | ||
(10%Depreciation on machinery recorded) | |||
(h) | No Entry | ||
(i) | W.I.P | 42,000 | |
F.O.H Applied | 42,000 | ||
(F.O.H Applied 7000 hrs @ 6) | |||
(j) | Finished Goods | 215,000 | |
W.I.P | 215,000 | ||
(Finished Goods Cost recorded) | |||
(k) | General Ledger | 200,000 | |
Finished Goods | 200,000 | ||
(Cost of goods sold recorded) | |||
Total | 785,300 | 785,300 |
Q.6: Calculate the normal and overtime wages payable to a worker for the following data.
Q.6: Calculate the normal and overtime wages payable to a worker for the following data:
Days | Hours worked |
Monday | 10 |
Tuesday | 11 |
Wednesday | 9 |
Thursday | 12 |
Saturday | 40 |
Sunday | 4 |
Normal working hours were 8 hours per day. Normal rate was Rs. 10.00 per hour. Overtime rate was as follows:
Up to 9 hours in a day at single rate and over 9 hours in a day at double rate or up to 48 hours at single rate and above it at double rate, which is more beneficial to the worker.
Solution:
Days | Hours Worked | Normal Hours Wage Abdullah @ 10 | Overtime Hours Wage @ 10 upto 9 hrs. | Overtime Hours Wage @ 20 more than 9 hrs. | Total Wage |
Monday | 10 | 80 | 10 | 20 | 110 |
Tuesday | 11 | 80 | 10 | 40 | 130 |
Wednesday | 9 | 80 | 10 | 0 | 90 |
Thursday | 12 | 80 | 10 | 60 | 150 |
Friday | 10 | 80 | 10 | 20 | 110 |
Saturday | 4 | 40 | 0 | 0 | 40 |
Total Weekly Wage | 630 |
Condition 2
Total Weekly Working Hours = 56
Single wage @ Rs. 10 per hour upto 48 hrs. = 48 x 10 = 480
Double wage @ Rs. 20 per hour for 8 hrs. = 8 x 20 = 160
Total Wage = 480 + 160 = 640
Conclusion: Under option 1, total wage is 630 whereas under option 2 total wage is 640 so option 2 is more beneficial for the worker.
Q.7: During January 2010, Department 2 received 20,000 units @ Rs. 19.50 from Department 1. Direct Labour of Rs. 36,284 and factory overhead of Rs. 72,568 were spend to process these units. During Processing 500 units were lost as unavoidable spoilage. 3,500 units estimated to be 80% completed, Were in process at the end of month. Remaining units were passed on to Department 3. Required: Cost of production report of December 2 and 31st January, 2010.
Solution:
XXX Company Department 2
Cost of Production Report
Month ended 31st Jan 2010
Quantity Schedule: | ||
Unit received from preceding department 1 | 20,000 | |
Units completed &transferred out to Department 3 | 16000 | |
Units still in process | 3500 | |
Units Lost in process (Abnormal unavoidable Spoilage) | 500 | |
20,000 | 20,000 | |
Break-up of 3500 units still in process: | ||
3500 x 0.80 = 2800 units completed | ||
Cost charged to department: | Total Cost | Per Unit Cost |
Cost from preceding department 20,000 x 19.50 | 390,000 | |
Cost added by Department: | ||
Labor | 36,284 | |
Factory overhead | 72,568 | |
Total Cost & Total Per Unit Cost | 498852 | 25.14 |
Cost accounted for as follows: | ||
Cost of units completed & transferred out to Department 3 (16,000 x 25.14) | 402240 | |
Cost of units still in process: | ||
Cost of 3500 units received from department 1 | ||
3500 x 19.50 = | 68,250 | |
Cost added by the department | ||
Labor 3500 x 0.80 x 1.88 | 5264 | |
FOH 3500 x 0.80 x 3.76 | 10528 | 84,042 |
Cost of Abnormal unavoidable loss: | ||
500 x 25.14 | 12570 | |
Total Cost accounted for | 498,852 |
Working 1: Equivalent Production:
Units Completed | 16000 |
Equivalent units WIP 3500 x 0.80 | 2800 |
Units spoiled | 500 |
Total completed units | 19300 |
Working 2: Per Unit Cost:
Labor | 1.88 |
Factory overhead (72568/19300) | 3.76 |
Q.8: Define the following term: (1) Conversion cost. (2) Job Order Costing (3) Semi-variable cost. (4) E.O.Q Economic Order Quantity. (5) Breakeven point.
Answer:
Conversion Cost
The total cost of direct labor and manufacturing overhead used to turn raw materials into finished items is known as the conversion cost. Direct material costs are not included in these charges. Wages paid to manufacturing staff as well as factory running costs including maintenance, utilities, and equipment depreciation are included in conversion costs. They are necessary for figuring out how much a product will cost to produce overall and for setting its price. Precise monitoring of conversion expenses aids companies in increasing productivity and efficiently allocating production funds.
Job Order Costing
An accounting technique called “job order costing” is used to monitor expenses related to individual projects or orders. This approach provides comprehensive cost information by allocating direct supplies, direct labor, and manufacturing overhead to each distinct operation. It is especially helpful in businesses like construction, printing, and specialty manufacturing when things are made to order. Job order costing guarantees correct invoicing to clients and assists firms in assessing the profitability of particular services. It also helps to improve cost control and find cost variances.
Semi-Variable Cost
An expense that has both fixed and variable components is referred to as a semi-variable cost, often called a mixed cost. The variable component varies in response to shifts in production volume or consumption, whereas the fixed portion stays constant independent of production or activity levels. A utility bill, which consists of a base price that is fixed and a use charge that is variable, is an example of a semi-variable cost. Businesses may partially manage expenditures with this kind of cost structure and remain flexible enough to adapt to changes in operational activity.
E.O.Q Economic Order Quantity
In inventory management, the Economic Order Quantity (EOQ) formula is used to find the ideal order size that minimizes the overall expenses of placing and maintaining inventory. It seeks to strike a balance between holding costs—the expenses related to keeping and storing inventory—and ordering costs, which are incurred each time an order is placed. Businesses may save inventory costs, prevent stockouts, and enhance overall inventory management efficiency by using the EOQ method. Businesses may attain cost-effective inventory levels and optimize their supply chain processes by figuring out the optimal order quantity.
Formula for Economic Order Quantity
\[ \mathbf{E.O.Q\ or\ Q =}\sqrt{\frac{\mathbf{2}\mathbf{DS}}{\mathbf{H}}}\ \]
Where D is Demand, S is S is ordering Cost and H is Holding or carrying cost
Breakeven Point
The breakeven point is the level of sales at which total revenues equal total costs, resulting in neither profit nor loss. It is a critical financial metric that helps businesses understand the minimum sales volume needed to cover all fixed and variable expenses. At the breakeven point, a company’s total contribution margin (sales revenue minus variable costs) exactly offsets its fixed costs. Calculating the breakeven point aids in decision-making regarding pricing, budgeting, and financial planning, ensuring that a business can determine the viability and profitability of its operations.
You might be interested in the following:
- 1. Material Costing, Specific Identification Method, Weighted Average Cost Method, First In, First Out Method(FIFO), Last In, Fist Out Method(LIFO)
- 2. Material Costing, Economic Order Quantity EOQ, Reorder Point/Ordering Point, Lead Time, Maximum Level of Inventory, Minimum Level of Inventory, Average Stock Level, Safety Stock, Danger Level, Optimum number of Orders, Order Frequency